

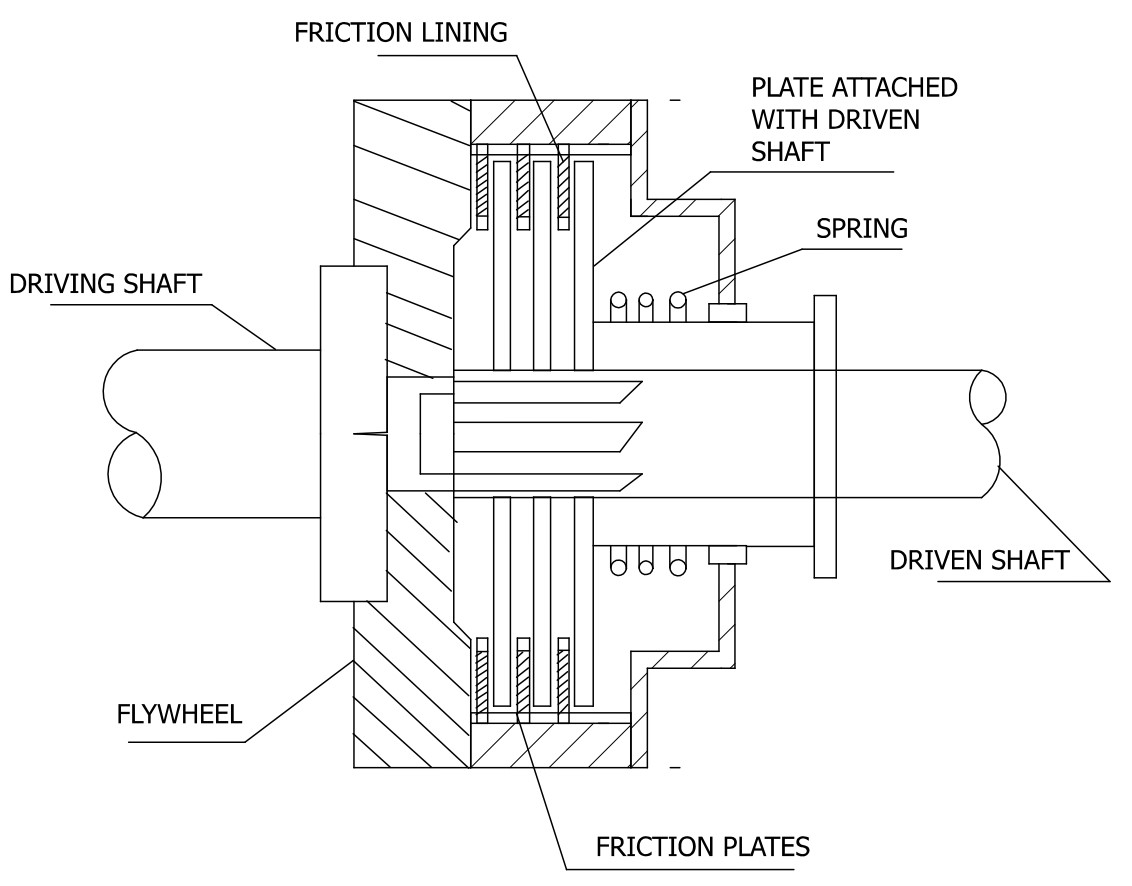
Groundcare equipment – rotary and flail mowers, turf cutters and scarifiers.They are commonly found on mobile equipment with rotating parts that are driven by small diesel or petrol engines. Depending on the design of the machine the output from the clutch can be one of a variety drives, including but not limited to shaft, pulley, sprocket or flange.Ī centrifugal clutch can be useful for a range of engine driven equipment with a high starting inertia. The springs, flyweights and the friction material are responsible for determining the speed at which the clutch engages. The rotation of the hub forces the shoes or flyweights outwards until they come into contact with the clutch drum, the friction material transmits the torque from the flyweights to the drum. When the crank shaft rotates the shaft of the clutch rotates at the same speed as the engine. One of the most common methods is by mounting the clutch onto the parallel or taper crank shaft of the engine. The clutch can be driven by a number of ways depending upon the design of the machinery. The centrifugal force, created by the revolutions of the engine is transmitted through two or more flyweights. The key components of a centrifugal clutch are the hub, flyweights (clutch shoes), springs, linings and housing (shown in the diagram below). Meaning this pre-set engagement speed cannot be changed without altering internal components.Ī centrifugal clutch works, as the name suggests, through centrifugal force. This allows the engine of the machinery to be running but without necessarily operating.ĭue to the nature of centrifugal clutch being a purely mechanical automatic engagement at a pre-determined speed, each application may require a specific configuration. In addition to providing a no-load situation the set engagement speed of the clutch also allows the operator to control at what point the rotary equipment becomes engaged. The wearing parts of a clutch are easy and cost effective to replace. By using a centrifugal clutch, this can be avoided as the components of the clutch will take the overload. This can be a very costly and sometimes economically unfeasible to repair the equipment. In circumstances such as this, for example when the rotating equipment is for some reason jammed, the extreme levels of torque transmitted back through the engine can cause significant and in some cases irreparable damage to the engine. It also helps protect the engine by ensuring high levels of torque are not transmitted back through the flywheel of the engine. This results in a smooth engagement and prevents the engine from stalling. Only when the rpm of the engine is increased to the set engagement speed of the clutch or above will the drive be fully connected. When the engine is idling the drive remains disengaged. Using a centrifugal clutch on engine driven equipment enables the engine to be started under a no-load situation. What Are The Advantages And Disadvantages Of Using A Centrifugal Clutch? This enables the operator to run the engine at a designated idling speed without driving the equipment, thus allowing the engine to reach its optimal torque before experiencing load. As the engine speed is increased to or above the set engagement speed of the centrifugal clutch the mechanical drive will become engaged. By using this type of clutch between the drive and the driven equipment the speed at which the mechanical driven shaft engages can be controlled. Most commonly used with a combustion engine, the clutch can be used to automatically transmit the torque from the drive to the driven equipment giving a “soft start” with no load engagement. A centrifugal clutch is a mechanical device which is used on driven rotary equipment.
